まずは動画をご覧ください
RBS工房について
・所在地: 神奈川県海老名市。
・活動内容: RBSの魅力を多くの人と共有することを目指して、制作活動を行っています。3D CAD、3Dプリンター、レーザーカッター、等のデジタルツールを活用しています。
・工房の中はこんな感じです。↓
左の3台が3Dプリンター、奥がCO2レーザー加工機です。
棚の上には仕掛かり品が多数。
反対側は作業スペースです。散らかってます..(^^;
制作者プロフィール
某社のIT部門に勤務。
・2015年以前: RBSに関心を持ちながらも、一品物を作成する技術も時間もなく、たまに少しトライしてはあきらめることを繰り返す。
・2016年: 3Dプリンターが普及価格になってきたこともあり調べていたところ、これならRBSを作れるかもしれないとひらめき1台購入。その後しばらく試行錯誤の連続。見よう見まねで色々なものを作成。3D CADの利用技術習得に注力。失敗を繰り返しながらも少しずつスキルアップ。
・2017年: アクリルケースに入った一連の作品の制作開始。アクリル板加工用に小型のレーザーカッターを導入。
・2018年: 制作活動を加速。露出用の4モデルを制作。フリマで個別販売開始(台数は限定的)。制作台数の増加に伴い3Dプリンターを追加導入(計3台稼働中)。Webによる作品情報の発信を開始。
・2019年: CO2レーザー加工機を導入。透明アクリルの加工が可能になったので、作品への展開を進める。作品は木質調+白色を基本とする方向へ。(多色展開はオプションで)
7月からWebショップを再オープン。多少の在庫ができるように順次作品の制作を進めています。
・2020年: 3〜4モデル/年のペースで作品の制作を継続。初の商用施設向けの作品も制作し納入(同作品は現在も稼働中)。
・2021年〜: よりデザイン性の高い作品を目指して作品の制作を継続中。
制作工程について
RBSの制作工程を紹介します。RBSは一般的にはステンレスワイヤーを曲げて、溶接して作成する作品が多いですが、私は3Dプリンターを使って必要なパーツを造形しています。
(1)最初に作品のイメージを考えながらRBSのラフスケッチを紙に描きます。
ここでは全体形状と以下のような基本構造を決めます。
・テーブルトップ型にするか、壁掛け型にするか、等の基本タイプの決定
・ボールのリフト方式をホイール、スクリュー、階段、チェーンベルト、から選択
・トラックの本数、ボールの大きさを決定
こんな簡単なスケッチから始まります。 ↓
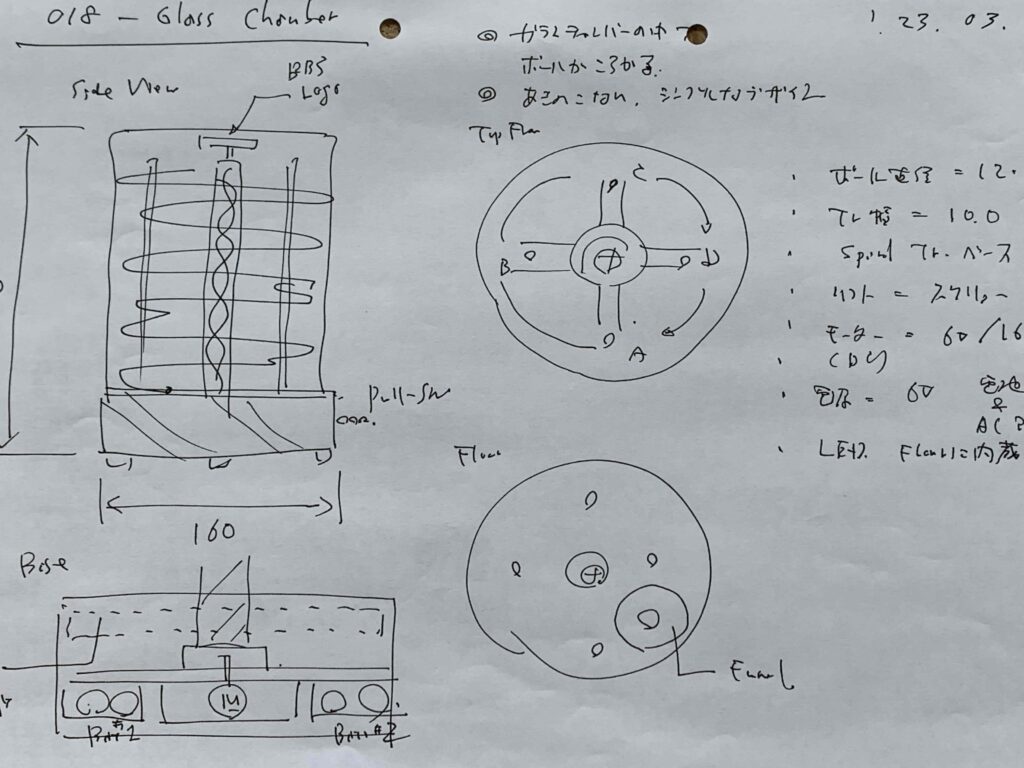
(2)次に、細部のデザインになりますが、各トラックのルーティングや、どんなギミックをつけるかを考えます。見て楽しいボールの動きになるように心掛けています。
この段階では紙に手書きで部品の寸法入り2D図面を描いていきます。特に注意するのはボールの落差(リフトされた頂上から、底部のドレインまでの距離)をどのように割り振るかです。トラックの長さ、形状、ギミックの種類でそれぞれ必要な高さがあります。各々の落差が十分でないとボールが途中で止まってしまったり、スピードが出すぎてトラック外に飛び出したりします。2D図面は最終的には、組み立て手順を書き加えた後に順番に並べて組み立てマニュアルとします。
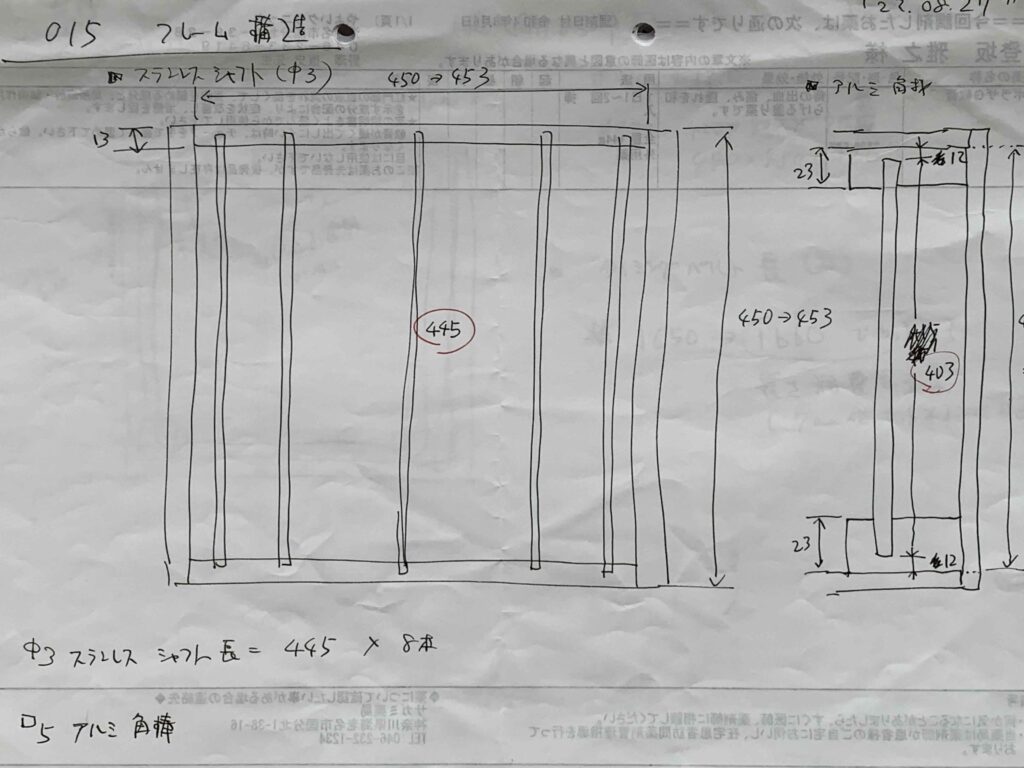
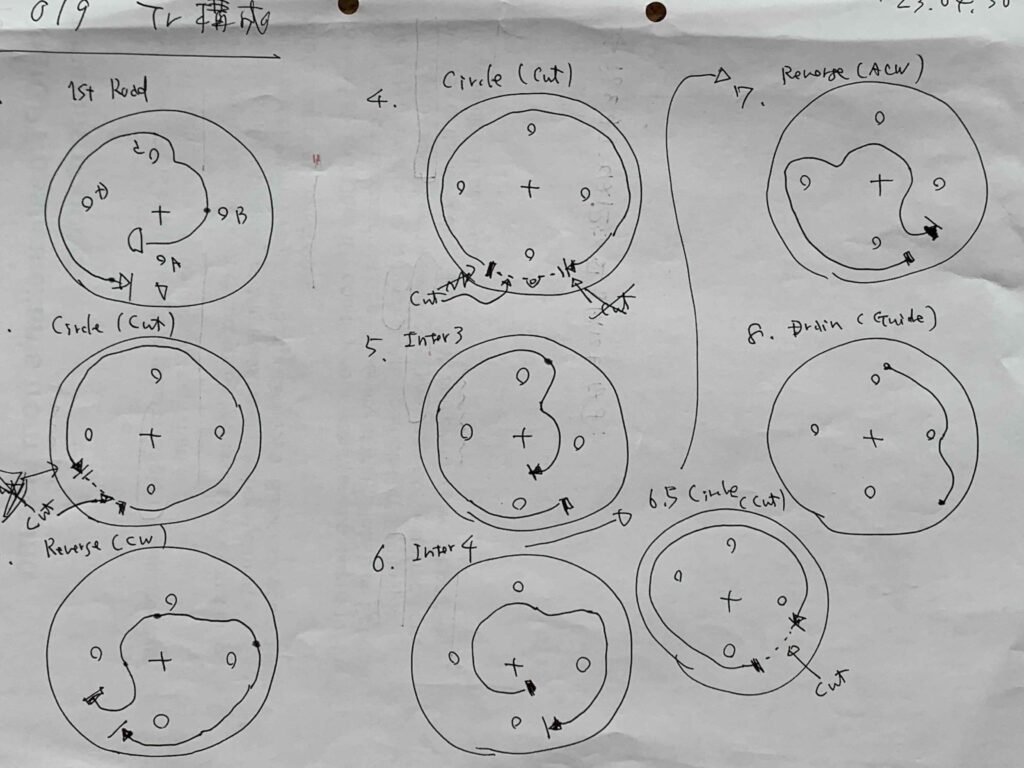
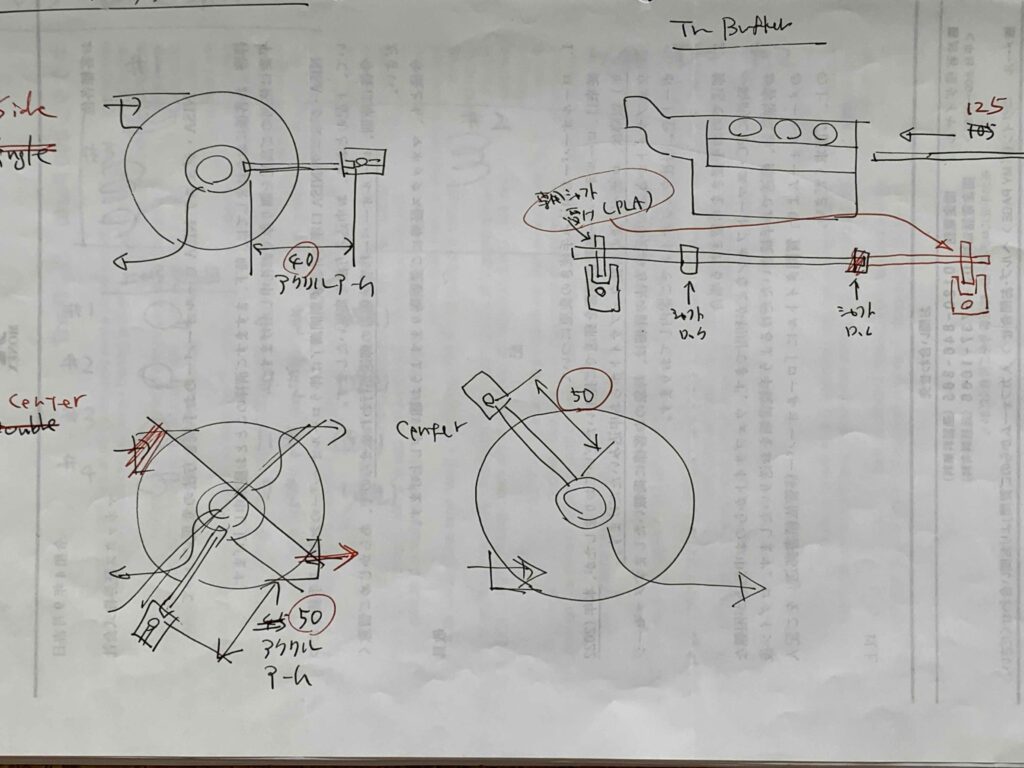
(3)この手書きの図面ができたらそれをもとに、3D CADで3D図面を書いていきます。RBSの構成部品はほとんどを3Dプリンターで出力していますので、外観や組立性を良くする為に、造形方向、連結部分の構造、サポート材の付く位置、等を考慮しながら設計していきます。設計が終わったら全ての部品を3D CAD上でアセンブリして、組立後の外観、寸法、部品間の干渉、ネジ穴の位置等を確認します。
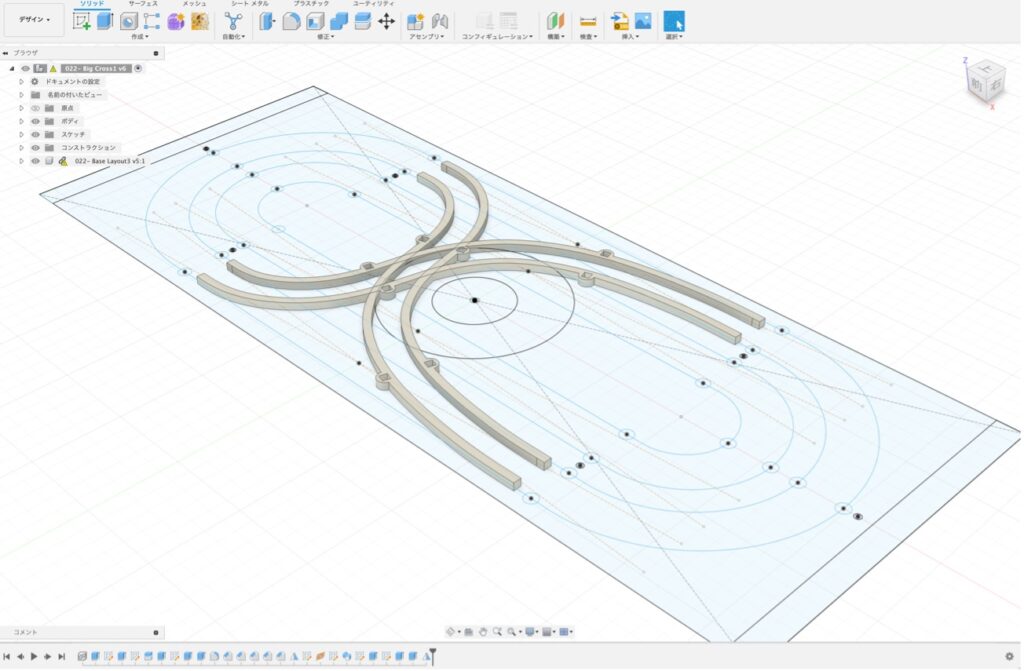
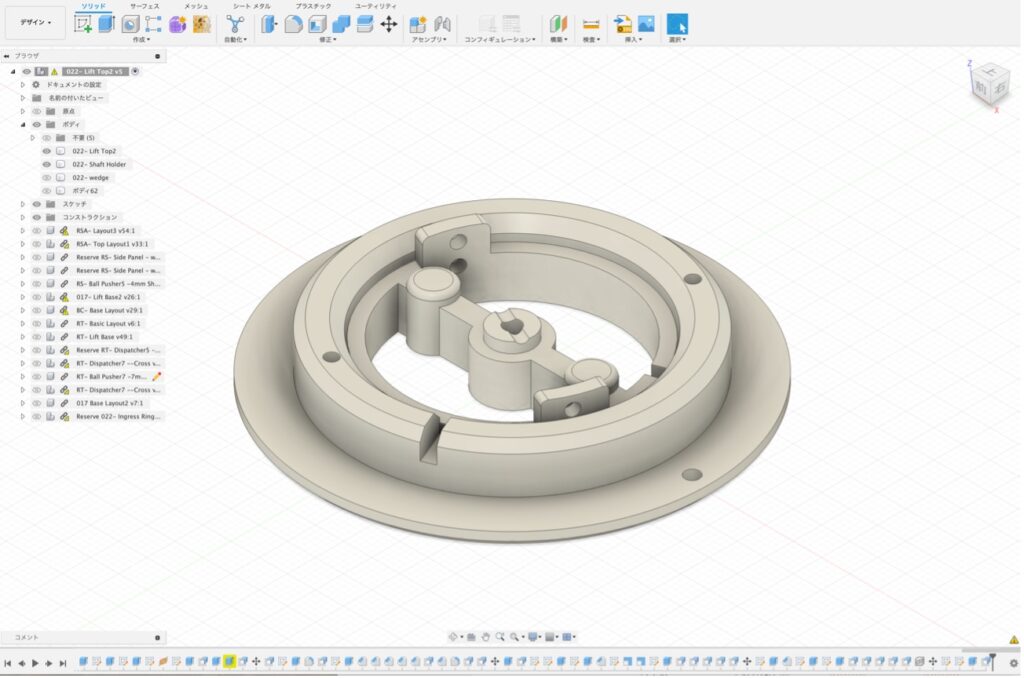
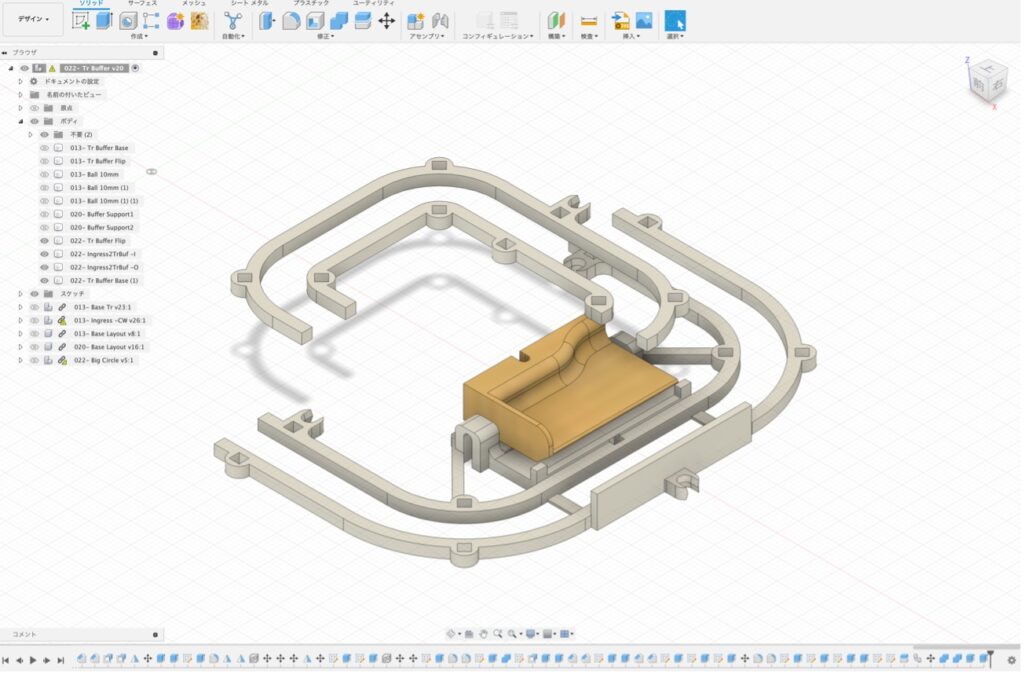
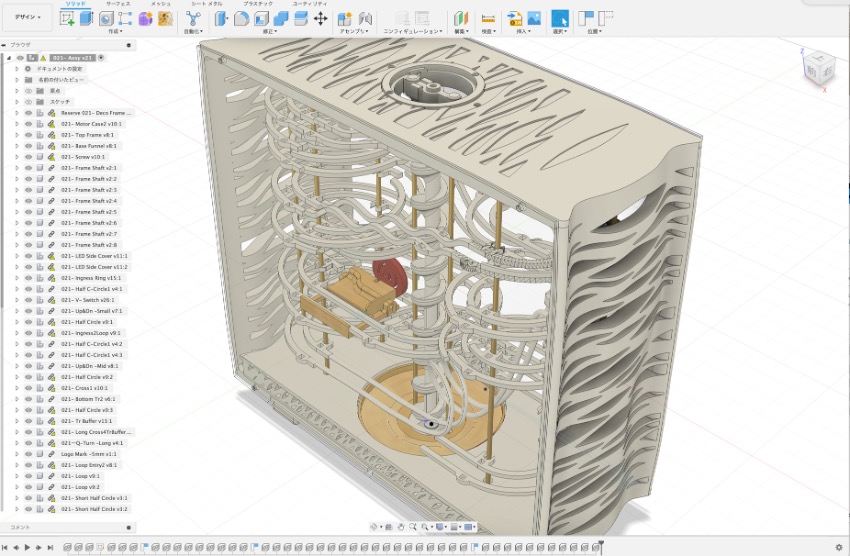
(4)部品を3Dプリンターで出力して、パーツを準備します。
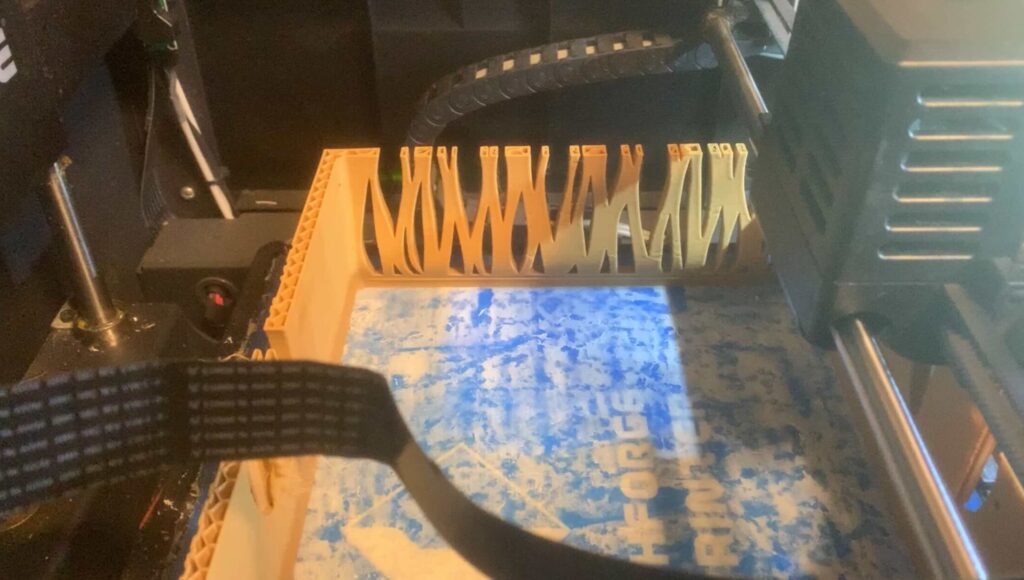
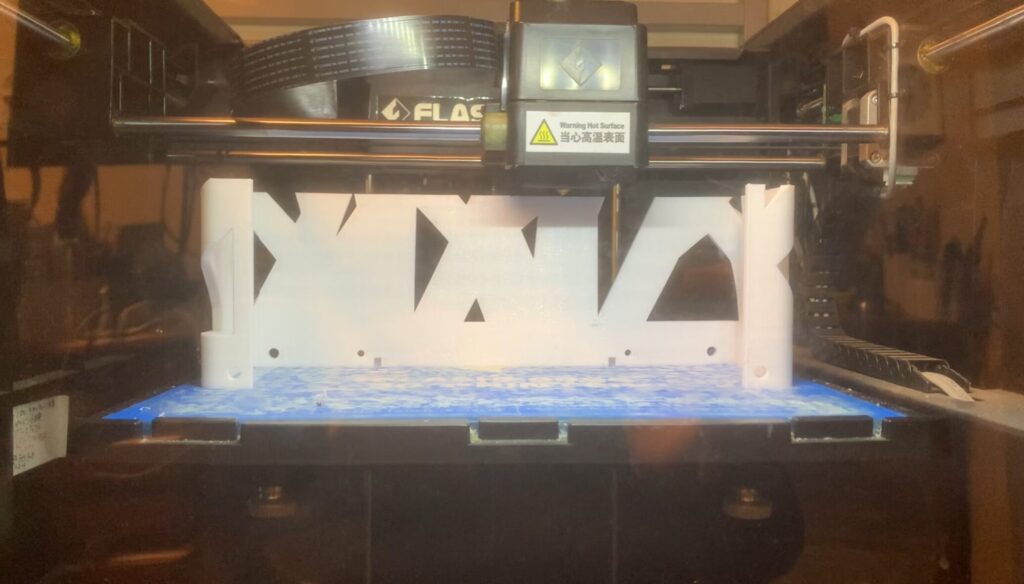
(5)パーツが揃ったら組み立てていきます。最初の評価/検証用のプロト機はすんなり動くことは少なく、寸法や取り付け角度を調整したりして修正を繰り返します。このようにして評価と修正を繰り返し、安定動作ができたら完成です。
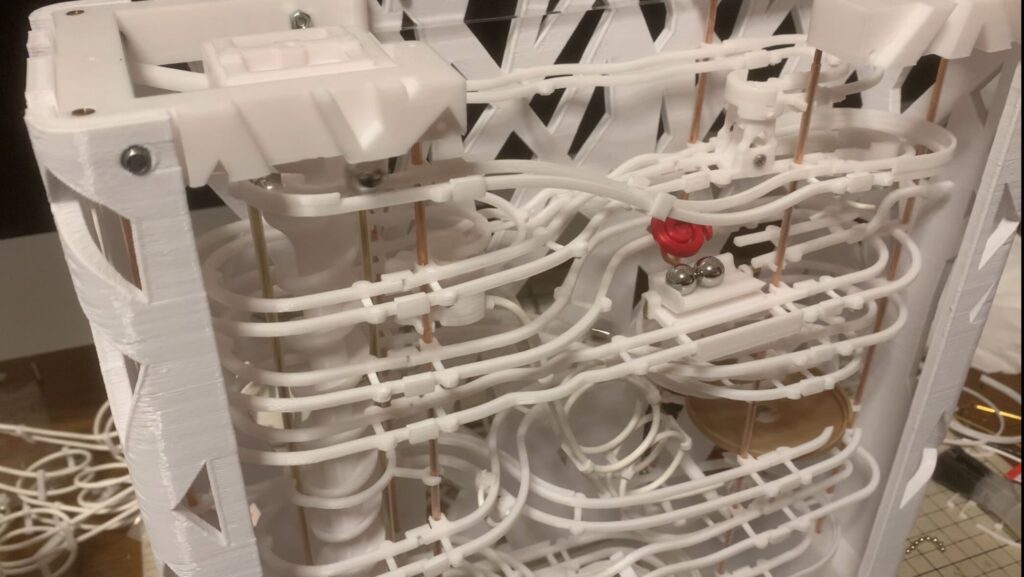
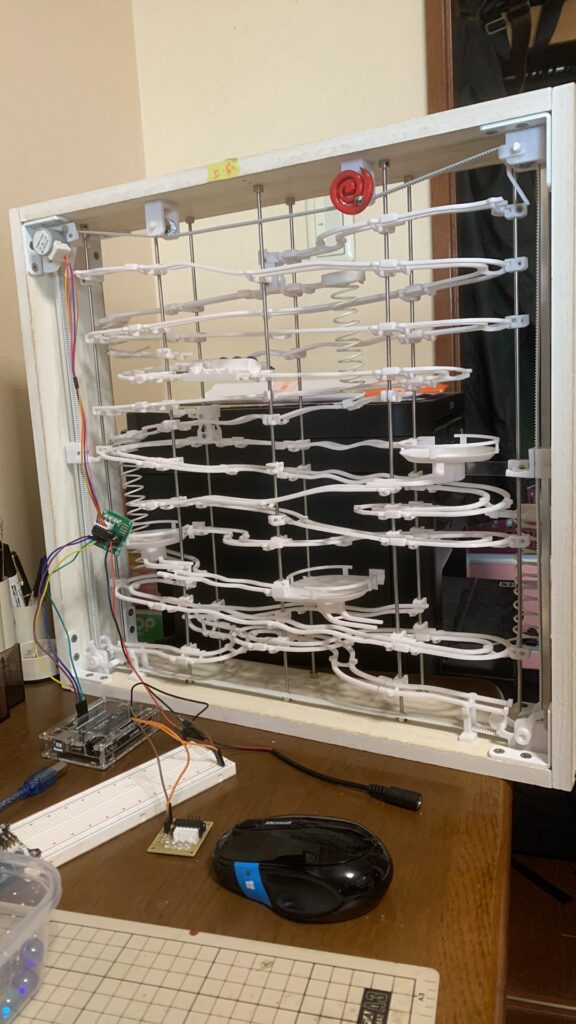
(6)安定化が完了したら、販売用の作品を順次制作していきます。
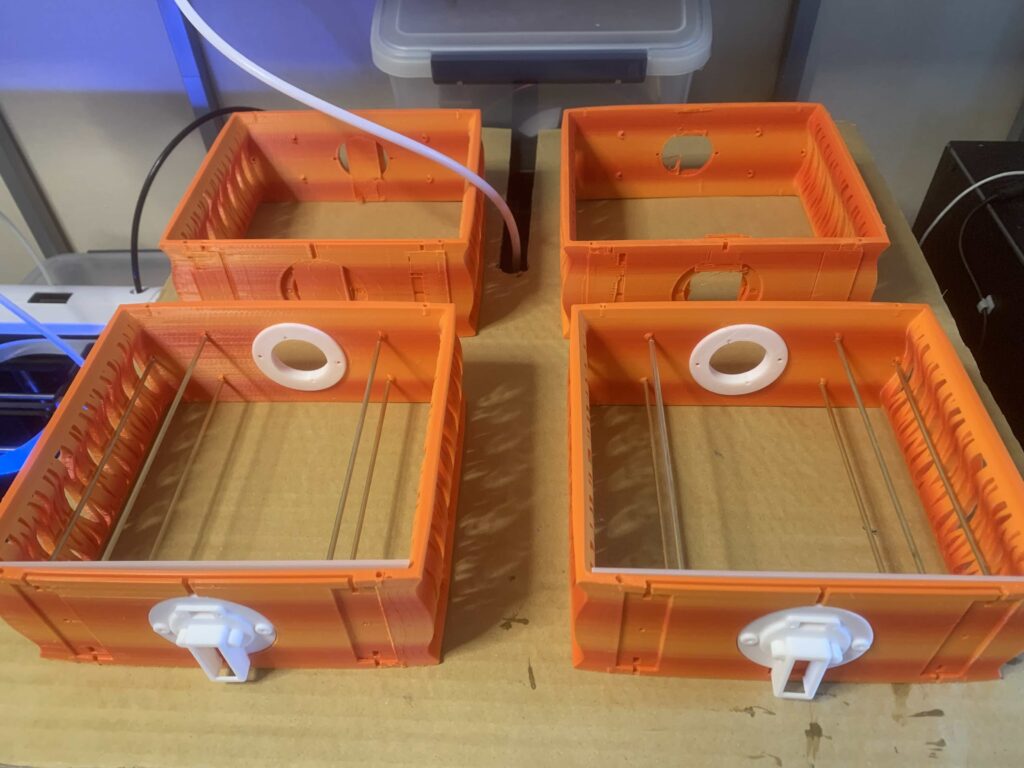
ーー